Pytanie 1
Na ilustracji jest przedstawione rozmieszczenie w magazynie grup zapasów wydzielonych na podstawie analizy ABC sporządzonej według kryterium
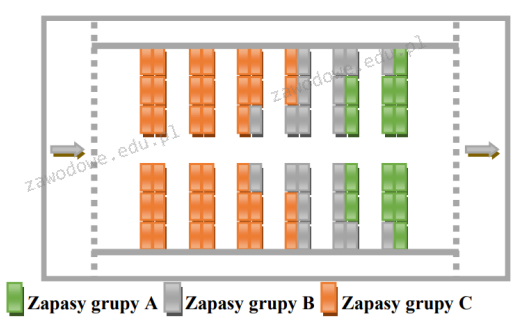
Wynik: 14/40 punktów (35,0%)
Wymagane minimum: 20 punktów (50%)
Na ilustracji jest przedstawione rozmieszczenie w magazynie grup zapasów wydzielonych na podstawie analizy ABC sporządzonej według kryterium
Ile sztuk opakowań o wymiarach 400x200 mm można umieścić w jednej warstwie na palecie EUR (1200 x 800 x 144 mm)?
Na podstawie danych zawartych w tabeli, oblicz procentowy udział opóźnionych dostaw w łącznej liczbie dostaw w roku 2013.
Lata | Łączna liczba dostaw | Liczba dostaw nieopóźnionych | Liczba dostaw opóźnionych |
---|---|---|---|
2011 | 50 | 40 | 10 |
2012 | 45 | 30 | 15 |
2013 | 60 | 45 | 15 |
Na rysunku przedstawiono
Na ilustracji jest przedstawione wnętrze magazynu
Jaką metodę określania rozmiaru dostaw należy zastosować, jeśli mają one charakter cykliczny, dostępne środki transportu mają ustaloną nośność, a dostawca ustalił minimalną wielkość partii do wydania?
Jaki system informatyczny jest używany do zarządzania obiegiem zapasów w magazynach?
To pytanie jest dostępne tylko dla zalogowanych użytkowników. Zaloguj się lub utwórz konto aby zobaczyć pełną treść pytania.
Odpowiedzi dostępne po zalogowaniu.
Wyjaśnienie dostępne po zalogowaniu.
Hurtownia produktów spożywczych wdrożyła system wolnych miejsc składowania, co umożliwiło przechowywanie towaru
Kierownik magazynu jest odpowiedzialny m.in. za
Przedstawiony piktogram informuje, że mamy do czynienia z materiałem
Do elementów obsługi klienta, które występują po zakończeniu transakcji, zalicza się
To pytanie jest dostępne tylko dla zalogowanych użytkowników. Zaloguj się lub utwórz konto aby zobaczyć pełną treść pytania.
Odpowiedzi dostępne po zalogowaniu.
Wyjaśnienie dostępne po zalogowaniu.
Realizacja procesu wytwórczego dla produktu końcowego, który nie był dotąd produkowany, na podstawie zamówienia klienta, stanowi zaopatrzenie materiałowe do produkcji
Analizowana i uśredniona wielkość dostaw lub wartość sprzedaży to
Odpady z plastiku należy wrzucać do pojemników w kolorze
Przedsiębiorstwo zajmujące się spedycją i transportem otrzymało zlecenie na transport ozdób choinkowych w 136 kartonach o wymiarach 800 x 600 x 1000 mm. Jeśli jedna naczepa może pomieścić 34 palety EURO, a palet i kartonów nie wolno układać na sobie, to towar powinien zostać załadowany do
Materiały, które najczęściej są wykorzystywane w procesie produkcji, powinny być przechowywane w magazynie producenta jak najbliżej strefy
Standardowym identyfikatorem używanym do jednoznacznej identyfikacji jednostek logistycznych jest
Supply Chain Management (SCM) stanowi system informatyczny umożliwiający zarządzanie firmą w obszarze
W dziedzinie zarządzania logistycznego za kontrolowanie, organizację oraz nadzór nad przepływem materiałów w firmie odpowiedzialna jest funkcja
To pytanie jest dostępne tylko dla zalogowanych użytkowników. Zaloguj się lub utwórz konto aby zobaczyć pełną treść pytania.
Odpowiedzi dostępne po zalogowaniu.
Wyjaśnienie dostępne po zalogowaniu.
Jak nazywa się proces, w którym owoce tracą wodę podczas przechowywania w magazynie?
Akt administracyjny wydany przez ministra odpowiedzialnego za transport lub wskazany w ustawie organ lokalny, który pozwala na prowadzenie działalności gospodarczej w obszarze transportu drogowego, to
Do konstrukcji magazynowych półotwartych zalicza się
Spis inwentaryzacyjny powinien być przeprowadzany minimum raz w roku na podstawie bilansu
Specjalistyczna funkcja w magazynie, która polega na łączeniu produktów pochodzących z różnych zakładów w przesyłki według zamówień klientów, to
Który z systemów informatycznych wykorzystywany jest do zarządzania relacjami z klientami?
Jakie będzie pole powierzchni modułu magazynowego w przypadku prostopadłego ustawienia paletowych jednostek ładunkowych na paletach EUR oraz drogi manipulacyjnej o szerokości 2,8 m, uwzględniając luz manipulacyjny?
Wskaźnik, który ilustruje przeciętny stopień odchyleń rzeczywistych wartości cechy od średniej arytmetycznej, nazywany jest
Na podstawie danych zamieszczonych w tabeli, przedstawiających stan zapasu magazynowego wyrobów gotowych i materiałów w przedsiębiorstwie, oblicz zapotrzebowanie netto tego przedsiębiorstwa na materiały niezbędne do realizacji zamówienia na 2 500 szt. długopisów, składających się z obudowy, sprężynki i wkładu.
Wyszczególnienie | Zapas magazynowy [szt.] |
---|---|
Długopis | 100 |
Obudowa | 1 500 |
Sprężynka | 1 200 |
Wkład | 2 000 |
Zorganizowany ciąg działań związanych z obiegiem zasobów to
Transport realizowany pojazdem samochodowym, który jest zarejestrowany za granicą lub przez zagraniczne przedsiębiorstwo, pomiędzy miejscami znajdującymi się na terytorium Rzeczypospolitej Polskiej, nazywa się przewozem
Koszty związane z usługami magazynowymi, uzależnione od powierzchni zajmowanej przez zapasy oraz okresu ich przechowywania, to koszty
To pytanie jest dostępne tylko dla zalogowanych użytkowników. Zaloguj się lub utwórz konto aby zobaczyć pełną treść pytania.
Odpowiedzi dostępne po zalogowaniu.
Wyjaśnienie dostępne po zalogowaniu.
Technika związana z prognozowaniem wymagań w końcowych lokalizacjach sieci dystrybucyjnej to
Międzynarodowa organizacja non-profit, która zajmuje się tworzeniem standardów w obszarze zarządzania łańcuchem dostaw oraz popytem, to
Wpływ wartości oraz korzyści materialnych uzyskanych lub należnych w związku z prowadzoną działalnością logistyczną określamy jako
System komputerowy stworzony do zarządzania zasobami dystrybucji to system
Ile sztuk opakowań o rozmiarach 400 x 200 mm można ustawić w jednej warstwie na palecie EUR?