Pytanie 1
Który karton został poprawnie odłożony na regał magazynowy uwzględniając umieszczony na nim znak manipulacyjny?
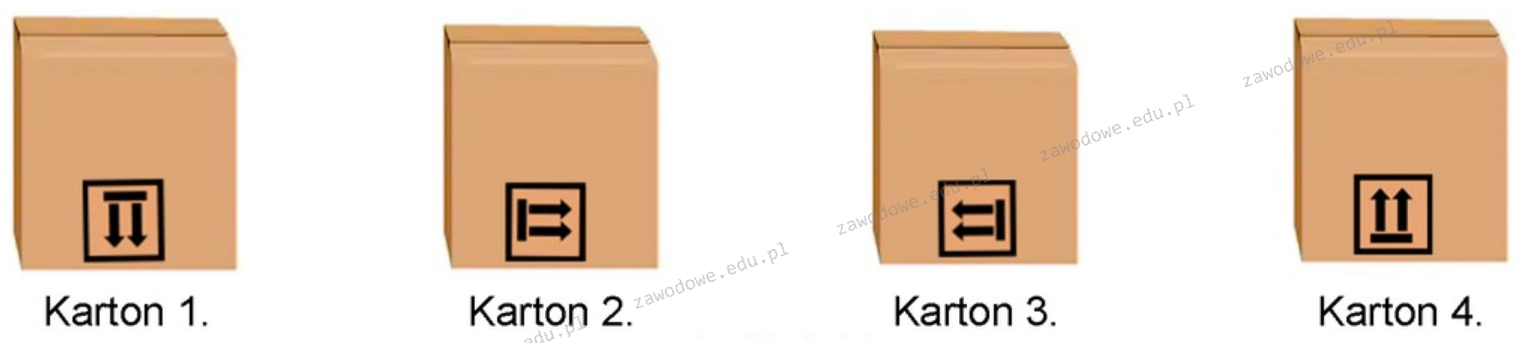
Wynik: 36/40 punktów (90,0%)
Wymagane minimum: 20 punktów (50%)
Który karton został poprawnie odłożony na regał magazynowy uwzględniając umieszczony na nim znak manipulacyjny?
Po przeprowadzonej inwentaryzacji stwierdzono niedobór zapasów o wartości 3 500,00 zł. Zgodnie z umową o wspólnej odpowiedzialności materialnej pani Patrycja Wolna zostanie obciążona kwotą
UMOWA O WSPÓLNEJ ODPOWIEDZIALNOŚCI MATERIALNEJ (fragment) | |
---|---|
1. | Pracownicy przyjmują łącznie wspólną odpowiedzialność materialną za szkody spowodowane niedoborem w powierzonym mieniu z obowiązkiem wyliczenia się. |
2. | Odpowiedzialność materialna pracowników w odniesieniu do każdego poszczególnego odpowiedzialnego materialnie pracownika wynosi Katarzyna Borowska – 35% poniesionej przez Pracodawcę szkody. Patrycja Kowalska – 30% poniesionej przez Pracodawcę szkody. Danuta Nowak – 15% poniesionej przez Pracodawcę szkody. Patrycja Wolna – 20% poniesionej przez Pracodawcę szkody. |
W magazynie, w którym wykorzystuje się wózki podnośnikowe, materiały zamawiane w największych ilościach powinny być rozsądnie rozmieszczone na regałach na
Który znak powinien być umieszczony na opakowaniach substancji żrących?
Prognozowane wydatki na magazynowanie, które zostały poniesione w maju 2012 roku w firmie "X", wyniosły 70 000 zł, natomiast wartość stanów z rejestrów magazynowych to 25 000 zł. Koszt magazynowania przypadający na jednostkę zapasu w maju 2012 roku wyniósł
Podstawową zasadą w zarządzaniu zapasami jest
Który znak umieszczany na opakowaniu zabrania podnoszenia wózkami ładunku podczas jego przemieszczania i transportu?
Najlepsze wykorzystanie przestrzeni magazynowej ma miejsce, gdy długość strefy składowania jest
W sytuacji, gdy jeden producent produkuje określony zestaw artykułów, który nie jest w stanie zaspokoić wszystkich potrzeb klientów, rolą dystrybucji jest zrekompensowanie braku
Na ilustracji jest przedstawione stanowisko pracy
Zasada, według której ostatnie miejsce otrzymuje harmonogram dostaw gotowych produktów do klientów, a materiały do produkcji są pobierane (ssane) z wcześniejszych miejsc, opisuje system zarządzania przepływem materiałów
Oznaczenia przeciwpożarowe w magazynie to znaki
Na dzień 1 maja stan magazynowy materiału X wynosił 250 kg, natomiast w ciągu miesiąca do magazynu dostarczono dodatkowe 500 kg materiału X. Od 1 czerwca rozpoczęto produkcję, w której potrzebne jest utrzymanie zapasu na poziomie 800 kg materiału X. W magazynie wystąpił
Zarządzanie zapasami przez producenta, kiedy dostawca wybiera moment i treść dostaw, co zapewnia całkowitą dostępność towarów, to proces
Który dokument jest niezbędny do dokonania przyjęcia towaru do magazynu?
Podstawowe urządzenie przeznaczone do przechowywania towarów w magazynie o złożonej i wielopoziomowej konstrukcji to
Materiały, które najczęściej są wykorzystywane w procesie produkcji, powinny być przechowywane w magazynie producenta jak najbliżej strefy
Ile wynosił zapas początkowy wyrobu X w magazynie, mając na uwadze, że jego stan końcowy to 20 sztuk, przy czym do magazynu dostarczono 100 sztuk, a z magazynu wydano 200 sztuk tego wyrobu?
Firma oferuje usługi typu "door-to-door" (od drzwi do drzwi). W tym celu korzysta z pojazdów o różnej ładowności. Do zalet tej usługi należy między innymi
Do funkcji związanych z potransakcyjną dystrybucją zalicza się
Na podstawie danych z tabeli określ, w którym tygodniu pracownik magazynu miał największą wydajność w stosunku do wydajności planowanej.
Tydzień | A. | B. | C. | D. | |
---|---|---|---|---|---|
Wydajność w szt./h | planowana | 100 | 120 | 120 | 100 |
rzeczywista | 110 | 120 | 110 | 105 |
Oblicz czas transportu przesyłki kurierskiej z miejsca A do miejsca B, jeśli dystans między tymi punktami wynosi 180 km, a średnia prędkość wynosi 75 km/h?
Rysunek przedstawia wózek
W magazynie przed przyjęciem znajdowało się 1 500 szt. towaru, a po przyjęciu 17 500 szt. Oblicz, jaka jest wartość średniego zapasu cyklicznego w tym magazynie, jeśli stanowi ona połowę wartości dostawy?
Firma złożyła zamówienie na 24 600 kg cukru w hurtowni. W momencie dostawy do magazynu przywieziono 33 paletowe jednostki ładunkowe (pjł) cukru. Cukier był zapakowany w worki o wadze 25 kg. Na każdej palecie worki z cukrem były zorganizowane w 8 warstwach, z 4 workami w każdej warstwie. W wyniku przeprowadzonej kontroli ilościowej magazynier powinien ustalić
Do jakich kosztów przypisuje się wydatki na utrzymanie magazynu?
Przedstawiony znak stosowany do oznakowania ładunku informuje o
To pytanie jest dostępne tylko dla zalogowanych użytkowników. Zaloguj się lub utwórz konto aby zobaczyć pełną treść pytania.
Odpowiedzi dostępne po zalogowaniu.
Wyjaśnienie dostępne po zalogowaniu.
System bezpośredniego przesyłania dokumentów handlowych między firmami to metodologia
Jakie towary powinny być zamawiane w oparciu o system zapasu jednookresowego?
Rozpoczynając pracę w magazynie meblowym z wysokim składowaniem, pracownik powinien założyć fartuch lub kombinezon roboczy oraz przede wszystkim
Korzystając z przedstawionego schematu, oblicz ile minimum kilogramów jabłek oraz marchwi należy zamówić, aby przedsiębiorstwo produkcyjne mogło zrealizować zamówienie na 1 500 sztuk soku w kartonie, jeżeli w magazynie znajduje się 150 szt. wyrobu gotowego oraz 13 kg jabłek.
Pojazd dostarczający 84 skrzyniopalety jabłek został podstawiony do rozładunku o godzinie 10:50. Wózek widłowy może zabrać 2 skrzyniopalety jednocześnie. Czas trwania jednego cyklu pracy wózka wynosi 3 minuty, przeprowadzenie kontroli jakościowej oraz ilościowej całej dostawy zajmuje 20 minut, a sporządzenie dokumentów przyjęcia dostawy trwa 15 minut. O której godzinie zakończy się przyjęcie jabłek do magazynu?
LIFO oznacza zasadę wydawania z magazynu towarów, które
Podmioty transportowe o ograniczonym zasięgu, działające w sposób ciągły, które są stosowane w transporcie wewnętrznym do przenoszenia ładunków oraz osób w pionie, poziomie i pod kątem, określamy mianem
Do podstawowych środków używanych do formowania pakietowych jednostek ładunkowych nie wliczają się
Materiałem wytworzonym w trakcie procesu produkcyjnego z myślą o sprzedaży jest
Opłaty za przejazd samochodem po drogach krajowych uzależnione są między innymi od
Zarządzanie dostępnością surowców do produkcji realizowane jest poprzez tworzenie sieci
Wybierz najtańszego przewoźnika do przewozu 30 paletowych jednostek ładunkowych (pjł) o masie 500 kg/pjł na odległość 200 km, korzystając z danych zawartych w tabeli.
Przewoźnik A | Przewoźnik B | Przewoźnik C | Przewoźnik D | ||||
---|---|---|---|---|---|---|---|
Maksymalna liczba pjł w pojeździe [szt.] | Cena [zł/km] | Masa przesyłki [t] | Cena [zł] | Odległość przewozu [km] | Cena [zł] | Liczba pjł [szt.] | Cena [zł] |
15 | 3,60 | do 7,00 | 400,00 | do 50 | 700,00 | 1 – 9 | 600,00 |
17 | 3,80 | od 7,01 do 16,00 | 900,00 | 50 – 100 | 1 000,00 | 10 – 20 | 900,00 |
32 | 4,60 | od 16,01 do 32,00 | 1 100,00 | ponad 100 | 1 100,00 | 21 – 30 | 1 200,00 |