Pytanie 1
Przedstawiony obok znak w przedsiębiorstwie logistycznym oznacza
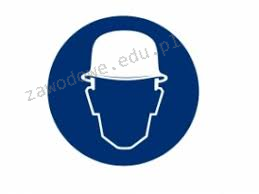
Wynik: 24/40 punktów (60,0%)
Wymagane minimum: 20 punktów (50%)
Przedstawiony obok znak w przedsiębiorstwie logistycznym oznacza
Zgodnie z zasadami BHP, drabiny powinny spełniać określone kryteria. Które z wymienionych kryteriów nie odnosi się do drabin?
Ile paletowych jednostek uda się załadować w ciągu pięciu dni, jeżeli magazyn funkcjonuje na trzech zmianach, a podczas jednej zmiany wydawanych i załadowanych na środki transportu jest średnio 320 pjł?
To pytanie jest dostępne tylko dla zalogowanych użytkowników. Zaloguj się lub utwórz konto aby zobaczyć pełną treść pytania.
Odpowiedzi dostępne po zalogowaniu.
Wyjaśnienie dostępne po zalogowaniu.
DRP zajmuje się prognozowaniem zapotrzebowania związanym
Rodzaj zarządzania w systemie logistycznym dotyczący obiegu informacji obejmuje
Podczas załadunku towaru pracownik uległ wypadkowi z podejrzeniem uszkodzenia kręgosłupa. Jakie powinno być pierwsze działanie polegające na udzieleniu pomocy poszkodowanemu przy ułożeniu go na twardym podłożu?
Jakie jest ograniczenie związane z ciągłą kontrolą zapasów?
Część rachunkowości, której celem jest analiza oraz dostarczanie informacji zarządowi firmy dotyczących organizacji pracy i wykonywania zadań gospodarczych, określamy mianem rachunkowości
Która metoda określania wielkości dostaw zapewni realizację dostaw odpowiadających przewidywanemu całkowitemu zapotrzebowaniu w zaplanowanym okresie dla towarów, które charakteryzują się niskimi kosztami utrzymania zapasów oraz wysokimi kosztami realizacji dostawy?
Na palecie EUR utworzono ładunek składający się z trzech warstw kartonów o wymiarach: 400 x 300 x 300 mm (dł. x szer. x wys.). Jaka jest wysokość paletowej jednostki ładunkowej?
Masa pojedynczych elementów składanych ręcznie przez jednego pracownika, w przypadku pracy na stałym stanowisku, nie powinna być większa niż
Walec z maszyny papierniczej w zapasach firmy zajmującej się produkcją papieru jest
Przykładem wydania zewnętrznego jest przeniesienie
System RFID do automatycznej identyfikacji rozpoznaje ładunki przy użyciu metod
W jakim rodzaju magazynu będzie przechowywany materiał sypki (kruszywo o różnych granulacjach) stosowany do wytwarzania betonu towarowego?
Ile czasu potrzeba na rozładunek jednego pojazdu z 34 paletowymi jednostkami ładunkowymi (pjł) przy użyciu dwóch wózków widłowych pracujących równocześnie, jeśli cykl podstawowy związany z rozładunkiem jednej pjł wózkiem wynosi 1,5 min, a podjazd samochodu pod rampę oraz przygotowanie go do rozładunku zajmie 10,5 minut?
Na którym rysunku przedstawiono worek jutowy?
Sprzętem, który pozwala na przechowywanie towarów z zachowaniem określonej wysokości nad podłożem, są
Przy wymianie zniszczonego elementu regału w magazynie wysokiego składowania, powinno się
Przedstawiony znak, umieszczony na opakowaniu produktu, informuje, że
Jaką wadą cross-dockingu, stosowanego w centrach dystrybucji, można wskazać?
To pytanie jest dostępne tylko dla zalogowanych użytkowników. Zaloguj się lub utwórz konto aby zobaczyć pełną treść pytania.
Odpowiedzi dostępne po zalogowaniu.
Wyjaśnienie dostępne po zalogowaniu.
System ERP w informatyce odnosi się do planowania
Który znak umieszczany na opakowaniu zabrania podnoszenia wózkami ładunku podczas jego przemieszczania i transportu?
Stolarz otrzymał zlecenie na wykonanie 100 sztuk stołów kuchennych. Zużycie lakieru wynosi 0,25 I na jeden stół. Ile lakieru należy zamówić do produkcji tych stołów, mając na uwadze, że w magazynie znajdują się: lakier - 5 litrów, stół kuchenny - 20 sztuk, a zapas bezpieczeństwa nie jest brany pod uwagę?
Oblicz wskaźnik jakości obsługi klienta, jeśli w magazynie ustalono, że całkowita liczba wydań wyniosła 35 000 sztuk, z czego: właściwa liczba wydań to 31 000 sztuk, a błędna liczba wydań wyniosła 4 000 sztuk?
Do obiektów magazynowych półotwartych zaliczają się
Jakie są negatywne aspekty transportu drogowego?
Do kategorii produktów biodegradowalnych należą artykuły wykonane
Logistyczny operator realizuje niewielkie zamówienia oraz częste dostawy materiałów do produkcji samochodów. Taki system cechuje się
Czym jest integracja w łańcuchu dostaw?
Odpady z plastiku należy wrzucać do pojemników w kolorze
Oblicz wielkość partii produkcyjnej na podstawie przedstawionego wzoru, jeżeli czas od pobrania materiałów do zakończenia produkcji (tpz) wynosi 27 minut, czas jednostkowy wytwarzania wyrobu (tj) wynosi 0,9 godziny, a wskaźnik (q) 0,05.
n = tpz q * tj [szt.] |
Dokumentem, który potwierdza przyjęcie materiałów do magazynu od dostawcy, jest
Jakie działania obejmuje proces przemiany surowców oraz materiałów w gotowe produkty?
To pytanie jest dostępne tylko dla zalogowanych użytkowników. Zaloguj się lub utwórz konto aby zobaczyć pełną treść pytania.
Odpowiedzi dostępne po zalogowaniu.
Wyjaśnienie dostępne po zalogowaniu.
Korzyści wynikające z ekonomii skali zakupów są uzyskiwane przez
Przedstawiona tabela zawiera dane dotyczące stanu zapasów oraz liczbę wyrobów gotowych montowanych w przedsiębiorstwie na dwóch zmianach. W związku z koniecznością realizacji 9 przenośników taśmowych, firma powinna zamówić
Elementy montażu | Stan zapasów w sztukach | Montaż wykonywany podczas I zmiany w sztukach | Montaż wykonywany podczas II zmiany w sztukach |
---|---|---|---|
silniki | 4 | 5 | 4 |
taśmy | 5 | 4 | 5 |
Zabieranie materiałów z głównego magazynu na potrzeby produkcji odbywa się na podstawie dokumentu