Pytanie 1
Ilu sztuk wyrobu gotowego brakuje do realizacji prognozy sprzedaży?
Magazyn | Zapas w szt. | Prognoza sprzedaży w szt. |
---|---|---|
ML1 | 20 | 40 |
ML2 | 10 | 30 |
ML3 | 10 | 30 |
MR | 10 | - |
MF | - | - |
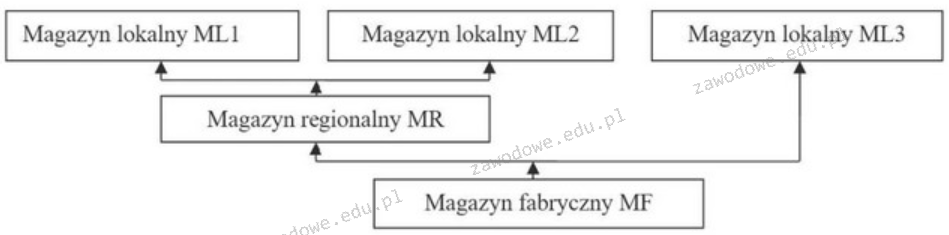
Wynik: 19/40 punktów (47,5%)
Wymagane minimum: 20 punktów (50%)
Ilu sztuk wyrobu gotowego brakuje do realizacji prognozy sprzedaży?
Magazyn | Zapas w szt. | Prognoza sprzedaży w szt. |
---|---|---|
ML1 | 20 | 40 |
ML2 | 10 | 30 |
ML3 | 10 | 30 |
MR | 10 | - |
MF | - | - |
Koncepcja, w ramach której towary dostarczone do terminala, niemal bez składowania, są natychmiast sortowane, dzielone na mniejsze partie, a po połączeniu z innymi towarami są przekazywane do różnych odbiorców, nazywana jest
Średnia wartość dostaw bądź przeciętna wartość sprzedaży, która podlega analizie i uśrednieniu, to
W porcie kontenerowym przyjęto ładunek drobnicowy w postaci 88 palet. Jak długo potrwa rozładunek towaru, jeśli do tego zadania wykorzystano 4 wózki widłowe, a cykl transportowy jednego wózka trwa 2 minuty?
Zadaniem funkcji potransakcyjnej w dystrybucji jest
W metodzie MRP, ilość wymaganych materiałów ustalana jest na podstawie
Na podstawie przedstawionego cennika oblicz koszt składowania 8 pustych kontenerów 20 ft i 6 pełnych kontenerów 40 ft w kontrolowanej temperaturze przez 4 dni.
Cennik | |
---|---|
Koszt składowania jednego pustego kontenera 20 ft: 30,00 zł/dzień | |
Koszt składowania jednego pustego kontenera 40 ft: 40,00 zł/dzień | |
Koszt składowania jednego pełnego kontenera 20 ft: 45,00 zł/dzień | |
Koszt składowania jednego pełnego kontenera 40 ft: 60,00 zł/dzień | |
Koszt składowania jednego pełnego kontenera 20 ft w kontrolowanej temperaturze: 70,00 zł/dzień | |
Koszt składowania jednego pełnego kontenera 40 ft w kontrolowanej temperaturze: 85,00 zł/dzień |
Kategoria produktów o małym udziale w ogólnej wielkości popytu na produkcję lub sprzedaż, generująca niskie przychody, to w klasyfikacji analizy asortymentu wyrobów
Dla artykułów, których długość znacząco przewyższa inne wymiary gabarytowe i wynosi więcej niż 1,2 m, tworzy się jednostki ładunkowe
W czasie inwentaryzacji w magazynie odkryto:
− brak 120 szt. konfitury truskawkowej po 2,50 zł/szt.,
− nadwyżkę 90 szt. konfitury wiśniowej po 2,60 zł/szt.
Komisja inwentaryzacyjna postanowiła zrekompensować niedobór konfitury truskawkowej nadwyżką konfitury wiśniowej. Wartość rekompensaty zgodnie z zasadą mniejsza ilość – niższa cena wyniesie?
Do zadań osób zajmujących się zarządzaniem stanami magazynowymi należy między innymi
Przedstawiony harmonogram czasu pracy kierowców ilustruje liczbę kursów realizowanych przez przedsiębiorstwo logistyczne w ciągu dnia. Wyznacz trasę kierowcy IV zakładając, że każdy z kierowców spędza jednakową liczbę godzin za kierownicą.
Trasa -X- 220 km | Trasa -Y- 280 km | Trasa -Z- 160 km | Trasa -L- 340 km | Trasa -K- 440 km | Trasa -M- 440 km | Średnia prędkość pojazdu na trasie w km/h |
---|---|---|---|---|---|---|
Kierowca I | ——— | Kierowca I | Kierowca I | ——— | ——— | 80 |
——— | Kierowca II | ——— | ——— | Kierowca II | ——— | 80 |
Kierowca III | ——— | Kierowca III | Kierowca III | ——— | ——— | 80 |
——— | ——— | ——— | ——— | ——— | ——— | Kierowca IV |
W ciągu jednej godziny przyzakładowa oczyszczalnia ścieków ma zdolność do oczyszczenia 1 000 litrów wody z zanieczyszczeń poprodukcyjnych. Ile litrów wody jest w stanie oczyścić ta oczyszczalnia w ciągu tygodnia, jeśli pracuje przez 20 godzin każdego dnia?
System łączący komunikację głosową oraz świetlną, w którym po uruchomieniu zlecenia miejsce składowania jest oznaczane ruchomym światłem, a informacja o liczbie przedmiotów do pobrania jest przekazywana przez słuchawki, określany jest jako
Którą z metod zarządzania wydaniami magazynowymi powinno się wdrożyć w mleczarni, kierując się zasadą 'pierwsze traci ważność, pierwsze opuszcza magazyn'?
W ciągu 50 s wózek widłowy, zarówno z ładunkiem, jak i bez, pokonuje przeciętnie 100 m. W trakcie wybranego cyklu wózek transportuje jedną paletę, czas, w którym wózek widłowy podejmuje ładunek, wynosi 5 s, a odległość do strefy regałowej to 50 m. Czas podnoszenia i odkładania palety na regał wynosi 15 s, a czas opuszczania wideł to 10 s. Ile czasu zajmie przemieszczenie 3 palet?
Jakie kryterium przy wyborze dostawcy powinno być kluczowe dla firmy, aby sprostać wymaganiom klienta w zakresie dostosowania terminu i metody dostawy, ilości partii oraz rodzaju towaru?
Który wydatek związany z zarządzaniem magazynem należy do kosztów zmiennych dotyczących uzupełniania stanów magazynowych?
Dostosowanie zewnętrznych rozmiarów opakowań transportowych do wymiarów przestrzeni ładunkowej palet, wymiarów wewnętrznych kontenerów oraz objętości ładunkowej stosowanych środków transportu to
Użycie przetworzonych olejów jako materiału do produkcji wysokiej jakości paliw określa się mianem
Wykorzystanie regałów przejezdnych torowych w obszarze składowania umożliwia zredukowanie nadmiaru
Który wózek widłowy powinien zastosować magazynier w celu umieszczenia paletowej jednostki ładunkowej w gnieździe regałowym na wysokości 1,9 metra?
Ustal koszt przewozu 15 palet wody mineralnej z zakładu produkcyjnego do odbiorcy oddalonego o 350 km, jeżeli firma transportowa ma następujący cennik przewozów:
1 – 5 palet: 1,50 zł/km |
6 – 10 palet: 1,70 zł/km |
11 – 15 palet: 2,00 zł/km |
16 – 25 palet: 2,30 zł/km |
Ile minimalnie wozów podsiębiernych, które transportują jeden kontener, powinien mieć terminal kontenerowy, zdolny do obsługi 60 kontenerów w ciągu godziny, przy założeniu, że średni czas pracy wozu podsiębiernego (podjazd po kontener, załadunek, transport, rozładunek) wynosi 5 minut?
Jaki układ technologiczny magazynu przedstawiono na schemacie?
Zespół jednostek handlowych, stworzony w celu magazynowania, przewozu oraz dla identyfikacji i monitorowania w łańcuchu dostaw, to jednostka
Wykorzystanie strategii Just in Time (czyli dokładnie na czas) pozwala między innymi na zarządzanie
Firma oferująca zróżnicowane usługi logistyczne, zazwyczaj w postaci pakietów zawierających między innymi: usługi transportowe, obsługę terminali, dystrybucję oraz magazynowanie, a także powiązane usługi informacyjne i finansowe, określana jest mianem przedsiębiorstwa
Powierzchnia składowa magazynu wynosi nominalnie 895 m2. Po umiejscowieniu regałów, łączna powierzchnia składowa zajęta przez magazyn wyniosła 823,4 m2. Jaki wskaźnik wykorzystania powierzchni składowej osiągnie ten magazyn?
Aby wyprodukować zamówione 5 000 sztuk skrzyń, potrzebne jest 2 500 m2 płyty. W magazynie jest dostępnych 1 000 m2, a w trakcie produkcji znajduje się jeszcze 800 m2. Ile należy zamówić płyty, aby zrealizować planowaną produkcję?
Zbiór firm współdziałających w procesie dostarczania towarów od producentów do różnych odbiorców to
Średnie zapotrzebowanie miesięczne wynosi 100 kg. W pierwszym tygodniu zapotrzebowanie osiągnęło 110 kg, a w drugim 90 kg. Wskaźniki sezonowości dla tych tygodni przedstawiają się odpowiednio
W magazynie ustalono limit ubytków naturalnych na poziomie 1,5% wartości rocznego obrotu magazynowego w roku poprzedzającym rok, na który zostaje ustalony limit ubytków. Zgodnie z danymi zawartymi w tabeli wartość niedoborów mieszczących się w granicach normy ubytków naturalnych w 2019 r. wyniosła
Zestawienie rocznych obrotów magazynowych | ||||
---|---|---|---|---|
Wyszczególnienie | Rok 2017 | Rok 2018 | Rok 2019 | Rok 2020 |
Obrót magazynowy | 360 tys. zł | 340 tys. zł | 420 tys. zł | 480 tys. zł |
Jakie elementy wchodzą w skład obszaru portowego?
Korzystając z danych zawartych w tabelach, wskaż warunki przechowywania jaj w pomieszczeniach magazynowych.
Wymagania dotyczące wilgotności względnej powietrza podczas przechowywania towarów | |
---|---|
Optymalna wilgotność względna powietrza | Rodzaj towaru |
85 ÷ 90% | kwiaty, świeże owoce i warzywa, mrożonki owocowe i warzywne, ryby |
65 ÷ 80% | jaja, miód |
60 ÷ 70% | mąka, cukier, sól, zboże, suszone owoce, papier, drewno |
50% | żelazo, wyroby metalowe, deski |
Wymagania dotyczące temperatury powietrza podczas przechowywania towarów | |
---|---|
Temperatura przechowywania | Rodzaj towaru |
20°C | mąka, cukier, sól |
15°C | oleje jadalne, deski |
4°C ÷ 10°C | margaryna, mleko |
3°C ÷ 10°C | masło, smalec, jaja |
0°C ÷ 10°C | owoce, warzywa |
-18°C ÷ -26°C | mrożone mięso wieprzowe, drób, ryby |
Zapas przechowywany w firmie, który jest wynikiem analizy ryzyka pojawienia się prognoz spekulacyjnych na rynku, to zapas
Na którym rysunku przedstawiono stojak do składowania towaru w beczkach?
Selekcja i pobieranie materiałów zgodnie z zamówieniami realizowane jest w obszarze
Termin planowanego przyjęcia towarów w lokalnym centrum dystrybucji ustala się, gdy stan magazynowy towarów będzie
Na podstawie cennika usług magazynowych oblicz, ile wyniesie całkowity koszt wynajęcia 350 m2 powierzchni budynków magazynowych zamkniętych i 300 m2 powierzchni placów składowych otwartych na okres dwóch miesięcy.
Powierzchnia | Magazyny zamknięte | Magazyny półotwarte | Magazyny otwarte |
---|---|---|---|
1 m² - 250 m² | 20 zł/m²/miesiąc | 15 zł/m²/miesiąc | 8 zł/m²/miesiąc |
251 m² - 500 m² | 19 zł/m²/miesiąc | 14 zł/m²/miesiąc | 7 zł/m²/miesiąc |
501 m² - 750 m² | 18 zł/m²/miesiąc | 13 zł/m²/miesiąc | 6 zł/m²/miesiąc |
751 m² - 1000 m² | 17 zł/m²/miesiąc | 12 zł/m²/miesiąc | 5 zł/m²/miesiąc |