Pytanie 1
Urządzenie przedstawione na rysunku służące do podtrzymywania towaru, na którym składowany asortyment opierany jest bezpośrednio o elementy konstrukcyjne, to
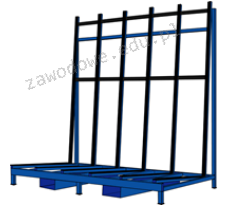
Wynik: 30/40 punktów (75,0%)
Wymagane minimum: 20 punktów (50%)
Urządzenie przedstawione na rysunku służące do podtrzymywania towaru, na którym składowany asortyment opierany jest bezpośrednio o elementy konstrukcyjne, to
Daty oraz ilości zamówień i dostaw stanowią fundament planowania
Wybrane standardy jakości owoców i warzyw do obrotu hurtowego zgodne z wymaganiami klientów Która dostawa nie spełnia gentlemenS agreements co do wielkości zepsutych produktów?
Partia jest zgodna ze standardem, gdy więcej niż 90% zawartości wszystkich opakowań spełnia wymagania:
Zgodnie z gentlemen's agreement (dżentelmeńska umowa) dopuszcza się u klienta do 2% zepsutych owoców i warzyw. |
Wykaz zrealizowanych dostaw
Masa zepsutych produktów [kg] | Wielkość dostawy | |
---|---|---|
Dostawa 1. | 22 | 40 skrzyń jabłek po 25 kg jabłek w skrzyni |
Dostawa 2. | 10 | 80 worków z ziemniakami po 50 kg ziemniaków w worku |
Dostawa 3. | 31 | 4 pjł z kapustą pekińską po 600 kg kapusty na palecie |
Dostawa 4. | 54 | 240 kartonów z pomidorami po 15 kg pomidorów w kartonie |
Użytkowanie regału magazynowego, który ma trwałe odkształcenia, jest dozwolone
System, w którym regularnie sprawdzane są zapasy i na podstawie tego ustalana jest ilość zamówienia, to system
W systemie numerycznym kodu kreskowego GS1, dwie, trzy lub cztery cyfry umieszczone w "()" wskazują na
Stałe zmiany wartości średniej badanej zmiennej zależnej (np. ciągły wzrost) w odniesieniu do innej zmiennej niezależnej (np. czas) określa się mianem
Magazyn wypożyczył 3 owijarki do palet oraz 2 urządzenia do taśmowania na okres 30 dni. Oblicz na podstawie zamieszczonego cennika wartość netto usługi wypożyczenia urządzeń.
Nazwa urządzenia | Jednostkowa cena netto* zł |
---|---|
Rampa mobilna | 100,00 |
Owijarka do palet | 80,00 |
Podnośnik stołowy | 50,00 |
Urządzenie do zgrzewania | 70,00 |
Urządzenie do taśmowania | 60,00 |
Podczas realizacji zadania w magazynie pracownik upadł, doznając złamania kości przedramienia. Jakie działania należy podjąć, aby udzielić poszkodowanemu pierwszej pomocy?
Która metoda składowania wyróżnia się najniższym wskaźnikiem użycia przestrzeni magazynowej?
W procesie transportu w magazynach wózki kolebowe, które są naładowane, stosuje się do przesuwania
Zestawienie produktów pochodzących z różnych zakładów w przesyłki zgodnie z zamówieniami klientów, z pominięciem etapu składowania, to
Ścieżkę realizacji działań produkcyjnych jako sekwencję zadań związanych z wytworzeniem gotowego produktu, według BOM, przedstawia
W pierwszym kwartale firma logistyczna poniosła wydatki rzędu 120 000 zł związane z zatrudnieniem 100 osób. W drugim kwartale przewiduje się redukcję zatrudnienia o 20%. Jeśli łączny koszt zatrudnienia nie ulegnie obniżeniu, to średni koszt zatrudnienia jednego pracownika w II kwartale wyniesie?
Na rysunku przedstawiono
Wizualną reprezentacją przedstawiającą klasyfikację ABC jest
Podstawowy system komputerowy stosowany w prognozowaniu zapotrzebowania na materiały w procesie produkcji?
Marszruta produkcyjna może być przedstawiona przy użyciu
Roczne wydatki na magazynowanie wynoszą 156 000 zł. Jakie są koszty związane z obsługą jednej palety w magazynie, jeżeli tygodniowy przepływ palet przez magazyn ustala się na 100 palet, a rok liczy 52 tygodnie?
Dokument dołączony do zamówienia na dostawę towarów, który potwierdza wcześniej ustalone warunki dostaw oraz płatności, to
RFID to technologia, która pozwala na monitorowanie przepływu towarów na podstawie
Rodzaj składowania, który umożliwia natychmiastowy dostęp do każdej jednostki ładunkowej w magazynie, określa się mianem składowania
Pojemnik elastyczny służący do przechowywania piasku określany jest jako pojemnik
Termin określający sytuację, w której towar dostarczony do magazynu jest natychmiast przekazywany dalej do odbiorcy bez etapu składowania, brzmi
Firma zajmująca się spedycją i transportem ma zrealizować zlecenie polegające na przewozie 396 palet z cegłą kratówką. Masa jednej paletowej jednostki ładunkowej wynosi 818 kg. Firma dysponuje pojazdami członowymi. Jedna naczepa może pomieścić 33 palety. Maksymalna ładowność naczepy to 27 040 kg. Ile pojazdów członowych będzie potrzebnych do wykonania usługi?
Przyjęcie towaru do magazynu dokumentuje się poprzez stworzenie odpowiedniego dokumentu
System HRM (Human Resource Management) obejmuje między innymi
System informatyczny wykorzystywany w centrum logistycznym do wspierania zarządzania relacjami z klientem, jest określany skrótem
Firma transportowa realizuje przewozy kontenerów na trasie Gdynia-Warszawa-Gdynia. W maju 2013 roku firma poniosła koszty stałe na wszystkie zrealizowane przewozy w kwocie 4 000 zł, a koszty zmienne wyniosły 3,50 zł za 1 km. Jakie były łączne koszty na 1 km, jeśli firma zrealizowała 10 kursów w obie strony, a odległość pomiędzy Gdynią a Warszawą wynosi 400 km?
W tabeli przedstawiono opisy zarządzania zapasami grup asortymentów. Który opis dotyczy klasyfikacji XYZ?
Opis A. | Opis B. |
Szybka reakcja na potrzeby konsumenta oraz maksymalna redukcja kosztów w całym łańcuchu dostaw. | Poziom utrzymania zapasów tworzą grupy: pierwsza I - największe zużycie, grupa II - średnie zużycie, grupa III - sporadyczne zużywane |
Opis C. Udział wielkości sprzedawanych grup asortymentowych w I kwartale 2009 przedstawiał się następująco: grupa I – 80%, grupa II – 15%, grupa III – 5% | Opis D. Planowanie potrzeb materiałowych na podstawie prognozowanego popytu. |
Klej stosowany do łączenia mebli drewnianych to
Firma zajmująca się logistyką planuje wprowadzenie systemu do zarządzania magazynem. Jaki to będzie system?
Który wózek widłowy, o najwyższym współczynniku wykorzystania jego udźwigu, należy zastosować do przewozu podczas jednego cyklu dwóch paletowych jednostek ładunkowych (pjł) o masie brutto 0,9 t/pjł?
Wózek widłowy 1. | Wózek widłowy 2. | Wózek widłowy 3. | Wózek widłowy 4. | |
Udźwig [kg] | 1 400 | 1 900 | 2 300 | 2 500 |
Firma transportowa "Smyk" używa następującego cennika przewozu: 1 - 10 palet: 2,00 zł/km, 11 - 21 palet: 2,50 zł/km. Jaką kwotę poniesie firma za transport 19 palet na trasie Poznań - Bydgoszcz (120 km)?
Identyfikacja towarów w sposób automatyczny wykorzystuje technologię
W przypadku poważnych oparzeń, które prowadzą do martwicy, czyli całkowitego zniszczenia wszystkich warstw skóry (skóra jest poparzona, czarna lub biała), należy
Magazyn jest przystosowany do przechowywania 2 120 paletowych jednostek ładunkowych (pjł). Na ogół w magazynie znajduje się 1 696 paletowych jednostek ładunkowych (pjł). Jakie jest współczynnikiem wykorzystania miejsc składowych w tym magazynie?
W tabeli przedstawiono dane o optymalnej wielkości i dynamice dostaw siewników dostarczanych w latach 2000 - 2004 do firmy zajmującej się sprzedażą sprzętu rolniczego. Określ metodę analizy, którą zastosowano przy obliczaniu wskaźników dynamiki.
Lata | Optymalna wielkość partii dostawy w szt. | Wskaźnik dynamiki % |
---|---|---|
2000 | 54 | - |
2001 | 60 | 111 |
2002 | 71 | 118 |
2003 | 77 | 108 |
2004 | 94 | 122 |
Czas trwania od rozpoczęcia zlecenia produkcyjnego do jego całkowitego zakończenia, obejmujący okres potrzebny na przygotowanie, uruchomienie, realizację oraz kontrolę, określa się mianem cyklu
Jakie urządzenia służą do układania paletowych jednostek ładunkowych na regałach w magazynach?