Pytanie 1
Który układ technologiczny magazynu i z wykorzystaniem której technologii składowania jest przedstawiony na rysunku?
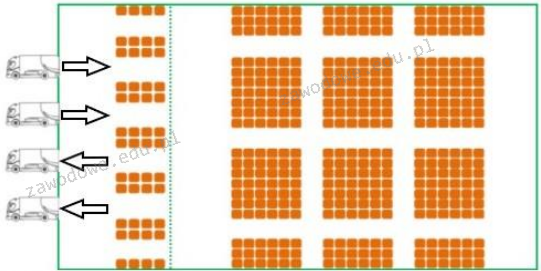
Wynik: 22/40 punktów (55,0%)
Wymagane minimum: 20 punktów (50%)
Który układ technologiczny magazynu i z wykorzystaniem której technologii składowania jest przedstawiony na rysunku?
Do systemów regałowych, których elementy konstrukcyjne są dostosowane do specyficznych właściwości składowanych produktów oraz technologii magazynowania, kwalifikują się regały
Do elementów wewnętrznych, które wpływają na wysokość kosztów logistyki w firmie, należą
Zastosowanie wielkości obrotu towarowego podczas planowania układu towarów w magazynie ma na celu
Zajęcie jednostek ochrony w firmie związane z potrzebami materiałowymi procesu produkcji określamy mianem
Jaką wartość zapasu informacyjnego należy utrzymać, aby złożyć zamówienie, jeżeli roczne zużycie surowca wynosi 61 920 sztuk, czas realizacji dostawy to 7 dni, a magazyn funkcjonuje przez 360 dni w roku?
Koszty związane z tworzeniem zapasów określamy jako wydatki
Złożono zamówienie na 160 sztuk długopisów. Cena brutto za jeden długopis wynosi 3 zł, a rabat udzielony na całe zamówienie to 15%. Podaj kwotę, na którą zostanie wystawiona faktura.
W zakładzie produkcyjnym opracowano plan wykorzystania przestrzeni magazynowej, który obejmuje następujące etapy. Do działań charakterystycznych dla etapu przyjęcia należą
Stolarz otrzymał zlecenie na wykonanie 100 sztuk stołów kuchennych. Zużycie lakieru wynosi 0,25 I na jeden stół. Ile lakieru należy zamówić do produkcji tych stołów, mając na uwadze, że w magazynie znajdują się: lakier - 5 litrów, stół kuchenny - 20 sztuk, a zapas bezpieczeństwa nie jest brany pod uwagę?
To pytanie jest dostępne tylko dla zalogowanych użytkowników. Zaloguj się lub utwórz konto aby zobaczyć pełną treść pytania.
Odpowiedzi dostępne po zalogowaniu.
Wyjaśnienie dostępne po zalogowaniu.
Model relacji biznesowych w internecie, który dotyczy realizacji transakcji elektronicznych między przedsiębiorstwami a klientem, nosi nazwę
Jaki jest wskaźnik niezawodności dostaw, jeżeli w trakcie miesiąca dokonano 50 dostaw, z czego 10 było niepełnych, a 2 z nich dotarły nieterminowo?
Podczas przeprowadzonej inwentaryzacji wykazano niedobór niezawiniony wynoszący 1 650 kg cukru, ewidencjonowanego po 2,00 zł/kg. Jaką wartość ma niedobór niezawiniony przekraczający normę ubytków naturalnych, jeśli limit ubytków wynosi 1% średniego rocznego obrotu magazynowego, który to obrót wynosi 300 000,00 zł?
W magazynach, w celu przesyłania rozmaitych dokumentów w formie elektronicznej, zamiast ręcznego wprowadzania ich do bazy danych, używa się systemu
Który dokument powinien być wpisany na schemacie w miejscu oznaczonym znakiem zapytania?
Firma złożyła zamówienie na 24 600 kg cukru w hurtowni. W dniu dostawy do magazynu przywieziono 33 paletowe jednostki ładunkowe (pjł) tego cukru. Cukier był pakowany w workach po 25 kg. Na każdej palecie worki z cukrem były ułożone w 8 warstwach, a w każdej warstwie znajdowały się 4 worki. Po przeprowadzeniu kontroli ilościowej magazynier zauważył,
Czym jest strategia "Pull"?
Koszty zmienne związane z utrzymaniem zapasu to wydatki
Kto ponosi odpowiedzialność za szkody powstałe w wyniku niewłaściwego transportu towarów?
Jakie będzie roczne wskaźnik kosztów utrzymania przestrzeni magazynowej, jeśli objętość użytkowa magazynu wynosi 2 500 m3, powierzchnia użytkowa magazynu to 400 m2, a całkowite roczne wydatki na magazynowanie wynoszą 280 000,00 zł?
Czas od momentu, gdy pojawia się potrzeba uzupełnienia zapasów, do chwili, gdy są one dostarczane i gotowe do użycia, to cykl
Dokument dołączony do zamówienia na dostawę towarów, który potwierdza wcześniej ustalone warunki dostaw oraz płatności, to
Wyznacz optymalną wielkość dostawy, biorąc pod uwagę planowany roczny popyt na poziomie 40 000 sztuk, koszt realizacji jednego zamówienia wynoszący 500,00 zł, cenę jednostkową równą 100,00 zł oraz wskaźnik rocznego kosztu utrzymania zapasów wynoszący 0,1.
Roczne wydatki na zatrudnienie pracowników w magazynie wynoszą 84 000 zł. Zazwyczaj w tym miejscu pracuje 6 osób. Jaki jest wskaźnik kosztów jednostkowych zatrudnienia, który umożliwia zaplanowanie budżetu na następny rok?
W tabeli przedstawiono procentowy udział różnych gałęzi transportu w przewozach ładunków w Polsce. Do opracowania wyników wykorzystano wskaźnik
Rok | transport | ||||
---|---|---|---|---|---|
2005 | kolejowy | samochodowy | rurociągowy | morski | śródlądowy |
w % | w % | w % | w % | w % | |
14,3 | 80,7 | 3,0 | 1,7 | 0,3 |
Jakie wskaźniki definiują udział czynności kompletacyjnych w ogólnych działaniach pracowników magazynowych?
Jakie towary powinny być zamawiane w oparciu o system zapasu jednookresowego?
Jeśli strefa składowania ma długość 24 m, szerokość 4 m oraz powierzchnię zajmowaną przez towary wynoszącą 48 m2, to w jakim stopniu wykorzystana jest ta strefa składowania?
Na koniec miesiąca hurtownia posiadała 34 000 sztuk towaru. W minionym miesiącu zrealizowano sprzedaż na poziomie 2 800 sztuk, a dostawy wyniosły 960 sztuk. Zgodnie z zasadą bilansującą, zapas towaru na początku badanego miesiąca wyniósł
Towary 1-2-3-4-5 rozmieszczono w magazynie według metody
1 | 4 | 3 | 2 | |
2 | 3 | 1 | ||
1 | 1 | 4 | 5 | |
5 | 4 | 2 |
Na rysunku przedstawiono
W sytuacji, gdy jeden producent produkuje określony zestaw artykułów, który nie jest w stanie zaspokoić wszystkich potrzeb klientów, rolą dystrybucji jest zrekompensowanie braku
Badanie analizy ABC dotyczącej zapasów w magazynie w celu ich właściwego rozmieszczenia w strefie składowania, mającego na celu zredukowanie czasu operacji manipulacyjnych, realizowane jest na podstawie kryterium
Na rysunku przedstawiono
Wskaż towary, które zaklasyfikujesz do grupy C według klasyfikacji ABC
Towar | Ilość | Cena | Wartość | Wartość narastająco | % narastająco |
---|---|---|---|---|---|
Masło | 1500 | 2,35 | 3525,00 | 3525,00 | 22,81 |
Cukier | 1125 | 2,10 | 2362,50 | 5887,50 | 38,09 |
Jogurt | 850 | 2,40 | 2400,00 | 7927,50 | 51,29 |
Kefir | 1300 | 1,60 | 2080,00 | 10007,50 | 64,75 |
Oliwa | 700 | 2,90 | 2030,00 | 12037,50 | 77,88 |
Ryż | 750 | 2,70 | 2025,00 | 14062,50 | 90,98 |
Miód | 88 | 12,30 | 1082,40 | 15144,90 | 97,99 |
Ocet | 70 | 2,30 | 161,00 | 15305,90 | 99,03 |
Sól | 120 | 1,25 | 150,00 | 15455,90 | 100,00 |
Jakiego rodzaju kanał dystrybucji wykorzystuje firma, gdy pomiędzy producentem a klientem znajduje się tylko jeden pośrednik?
Informatyczny system wspomagający zarządzanie magazynami, obejmujący zarówno stany towarów, ich lokalizacje, jak również kierowanie i nadzorowanie działań realizowanych w magazynie oraz w interakcji z produkcją, przyjęciami, wysyłkami i innymi procesami, to system
Obiekt magazynowy to miejsce ogrodzone, utwardzone, które nie jest osłonięte
Niewłaściwe zabezpieczenie zapasów przed działaniami chemicznymi może spowodować, że produkty będą