Pytanie 1
Na rysunku przedstawiono
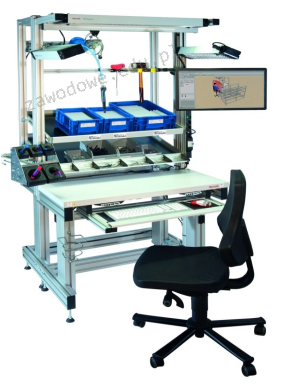
Wynik: 24/40 punktów (60,0%)
Wymagane minimum: 20 punktów (50%)
Na rysunku przedstawiono
To pytanie jest dostępne tylko dla zalogowanych użytkowników. Zaloguj się lub utwórz konto aby zobaczyć pełną treść pytania.
Odpowiedzi dostępne po zalogowaniu.
Wyjaśnienie dostępne po zalogowaniu.
Ilość wkrętów wytwarzanych w ciągu godziny przy użyciu frezarki wynosi 1 000 szt. Jak obliczyć wskaźnik wykorzystania potencjału produkcji frezarki, jeśli w czasie 8 godzin pracy na niej zrobiono 6 400 szt. wkrętów?
Sposób składowania zapasów w magazynie, w którym często pobierane towary umieszczane są w pobliżu strefy wydań, a rzadziej pobierane artykuły przechowywane są głębiej w strefie składowania, odpowiada kryterium
Czym jest rekultywacja?
To pytanie jest dostępne tylko dla zalogowanych użytkowników. Zaloguj się lub utwórz konto aby zobaczyć pełną treść pytania.
Odpowiedzi dostępne po zalogowaniu.
Wyjaśnienie dostępne po zalogowaniu.
Która z niżej podanych grup charakteryzuje zadania ekologistyki?
Grupa 1 | Grupa 3 |
|
|
Grupa 2 | Grupa 4 |
|
|
O czym informuje zamieszczony znak manipulacyjny, umieszczony na opakowaniu ładunku podczas transportu?
Samodzielne jednostki ekonomiczne nazywane węzłami logistycznymi, składające się z magazynów, terminali przeładunkowych oraz portów, połączone ze sobą siecią dróg tworzą
Rysunek przedstawia wózek
Na podstawie danych zawartych w tabeli ustal ekonomiczną wielkość dostawy.
Wielkość dostawy [kg] | Koszt utrzymania zapasu [zł] | Koszt uzupełniania zapasu [zł] | Całkowity koszt utrzymania i uzupełniania zapasu [zł] |
---|---|---|---|
75 | 260,00 | 185,00 | 445,00 |
50 | 240,00 | 160,00 | 400,00 |
25 | 195,00 | 195,00 | 390,00 |
10 | 170,00 | 240,00 | 410,00 |
W zamkniętym magazynie, w którym znajdują się środki do prania, umieszczono 50 pojemników z acetonem. Niewłaściwe warunki przechowywania mogą skutkować
Jaki dokument musi przygotować magazynier, aby zarejestrować przyjęcie zakupionych materiałów do magazynu?
Z jakiego dokumentu wynika przesunięcie surowców pomiędzy magazynami?
Podaj wymiary palety według normy ISO?
Zakład produkcyjny wytwarza codziennie 50 sztuk wyrobu X, którego skład obejmuje: 2 elementy Y oraz 3 elementy Z. Określ częstotliwość regularnych dostaw od dostawców elementów Y i Z, przy założeniu, że jednorazowa dostawa elementu Y wynosi 200 sztuk, a elementu Z 600 sztuk?
Jaką maksymalną liczbę kartonów o wymiarach 300 x 350 x 950 mm można ułożyć w jednej warstwie na palecie o wymiarach 1 200 x 1 000 x 150 mm?
Produkcja, która opiera się na częstych i niewielkich dostawach, redukcji zapasów oraz krótkich okresach realizacji zamówień, wpisuje się w założenia jakiej strategii?
Magazynier zatrudniony w firmie na akord w określonym miesiącu przepracował 23 dni. W każdym dniu zrealizował 25 zamówień. Stawka za realizację pojedynczego zamówienia wynosi 8,50 zł. Jeśli magazynier w ciągu miesiąca zrealizuje więcej niż 500 zamówień, przysługuje mu premia w wysokości 10% obliczana od wynagrodzenia za pracę akordową. Oblicz wynagrodzenie magazyniera za ten miesiąc.
Procedury, które należy stosować w przypadku pożaru, powinny być opisane w
Korzystając z danych zawartych w tabeli, ustal wielkość dostawy w czwartym okresie według metody stałej wielkości zamówienia.
Okres | 1 | 2 | 3 | 4 |
---|---|---|---|---|
Zapotrzebowanie [szt.] | 35 | 10 | - | 40 |
Wielkość dostawy [szt.] | 60 | - | - | ? |
Przekazywanie dóbr do odbiorcy zgodnie z zamówieniem odbywa się w obszarze
Korzystając z informacji w ramce, oblicz jaką minimalną liczbę sztuk wózków magazynowych należy przygotować, aby w czasie 2 godzin ułożyć 360 sztuk paletowych jednostek ładunkowych na regałach magazynowych. Cykl pracy wózka przy obsłudze 1 pjł obejmuje: podjęcie pjł, przewóz, odłożenie na regał, opuszczenie wideł, przejazd po kolejną pjł.
Wybrane parametry wózka magazynowego: |
- czas podjęcia pił do przewozu - 0,5 min. - czas przewozu pił ze strefy przyjęć do strefy składowania - 2 min. - czas odłożenia pił na regał - 1,0 min. - czas opuszczania wideł po odłożeniu pił na regał - 0,5 min. - czas przejazdu ze strefy składowania do strefy przyjęć po kolejną pił - 2 min. |
Towary są przygotowywane do magazynowania w etapie
Analiza metodą ABC/XYZ pozwala na klasyfikację asortymentu magazynowego w dziewięciu grupach. Towary należące do grupy CZ wyróżniają się
Jakim prefiksem posługuje się system kodów kreskowych EAN w Polsce?
W I kwartale firma logistyczna poniosła wydatki na zatrudnienie 100 pracowników w wysokości 120 000 zł. W II kwartale planowany jest spadek liczby pracowników o 20%. Przy założeniu, że łączne koszty zatrudnienia nie ulegną obniżeniu, ile wyniesie średni koszt zatrudnienia 1 pracownika w II kwartale?
Jaki będzie koszt transportu 30 paletowych jednostek ładunkowych (pjł) o wymiarach 1 200 × 800 × 500 mm (dł. x szer. x wys.), jeśli stawka za przewóz 1 m3 ładunku wynosi 150,00 zł?
Proces technologiczny, w ramach którego materiał niepełnowartościowy i uszkodzony został wykluczony z dalszej obróbki, pozwala na rejestrację
Nieregularna struktura procesu produkcyjnego cechuje się
W którym magazynie najlepiej wykorzystywana jest powierzchnia w strefie kompletacji?
Magazyn 1 | Magazyn 2 | Magazyn 3 | Magazyn 4 |
---|---|---|---|
Powierzchnia strefy kompletacji: 3 000 m2 | Powierzchnia strefy kompletacji: 3 500 m2 | Powierzchnia strefy kompletacji: 12 000 m2 | Powierzchnia strefy kompletacji: 9 000 m2 |
Średnia powierzchnia ładunku: 2 200 m2 | Średnia powierzchnia ładunku: 2 300 m2 | Średnia powierzchnia ładunku: 7 200 m2 | Średnia powierzchnia ładunku: 8 100 m2 |
A. | B. | C. | D. |
Który z systemów służy do zarządzania łańcuchem dostaw?
Niniejszy stan zapasów niezbędny do zapewnienia ciągłości produkcji w zakładzie wynosi 70 sztuk puszek. Ile sztuk nadwyżki zapasu ma zakład, jeśli na początku miesiąca stan magazynu wynosił 60 sztuk, a w trakcie kolejnego miesiąca zakupiono dodatkowe 30 sztuk puszek? Żadne z złożonych puszek nie zostały użyte w produkcji?
Gdy punkt, z którego realizowane jest zamówienie klienta, znajduje się w bliskiej odległości od klienta oraz rynku, to prawdopodobieństwo utraty zamówienia klienta
Kiedy firma podejmuje działania mające na celu rozwiązanie problemów oraz konfliktów ekologicznych w dziedzinie logistyki, to oznacza, że przestrzega zasad
Proces, który obejmuje wymianę informacji, transfer środków finansowych oraz transport towarów od dostawcy do odbiorcy, nazywany jest
Jaką czynność wykonuje się w obszarze kompletacji?
Na której ilustracji jest przedstawiony kod kreskowy QR?
Aby zabezpieczyć ładunek na palecie przed niekorzystnymi warunkami atmosferycznymi, należałoby użyć
Który wózek widłowy, o najwyższym współczynniku wykorzystania jego udźwigu, należy zastosować do przewozu podczas jednego cyklu dwóch paletowych jednostek ładunkowych (pjł) o masie brutto 0,9 t/pjł?
Wózek widłowy 1. | Wózek widłowy 2. | Wózek widłowy 3. | Wózek widłowy 4. | |
Udźwig [kg] | 1 400 | 1 900 | 2 300 | 2 500 |