Kwalifikacja: MTL.03 - Eksploatacja maszyn i urządzeń przemysłu metalurgicznego
W którym urządzeniu prowadzony jest proces redukcji bezpośredniej rud żelaza, przedstawiony schematycznie na rysunku?
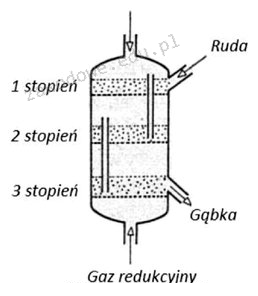
Odpowiedzi
Informacja zwrotna
Reaktor fluidyzacyjny jest kluczowym urządzeniem w procesie redukcji bezpośredniej rud żelaza, który polega na usunięciu tlenu z rudy, aby uzyskać metaliczne żelazo. W reaktorze tym ruda żelaza jest wprowadzana od góry, a gaz redukcyjny, zazwyczaj na bazie wodoru lub gazu naturalnego, jest wdmuchiwany od dołu. Takie podejście umożliwia optymalne wymieszanie rudy i gazu, co zwiększa efektywność reakcji chemicznych. Proces ten jest zazwyczaj bardziej efektywny niż tradycyjne metody, takie jak piec wysokotemperaturowy czy piec szybowy, ponieważ pozwala na niższe zużycie energii oraz ograniczenie emisji dwutlenku węgla. W praktyce, stosowanie reaktorów fluidyzacyjnych stało się standardem w nowoczesnym przemyśle metalurgicznym, w szczególności przy produkcji stali, co jest zgodne z najlepszymi praktykami branżowymi w zakresie zrównoważonego rozwoju i ochrony środowiska.
Wybór niewłaściwego urządzenia do procesu redukcji rud żelaza może wynikać z niedostatecznej znajomości technologii i zasad chemii stosowanych w metalurgii. Piec szybowy, choć szeroko stosowany w tradycyjnych procesach hutniczych, nie jest przystosowany do bezpośredniej redukcji rudy żelaza, gdyż jego działanie opiera się na procesie topnienia rudy z dodatkiem węgla, co prowadzi do produkcji żelaza w formie ciekłej. Użytkownicy mogą mylić piec szybowy z reaktorem fluidyzacyjnym, jednak różnią się one zasadniczo w podejściu do procesu. Retorta, z kolei, jest urządzeniem wykorzystywanym do przetwarzania surowców w stanach stałych, ale nie zapewnia odpowiednich warunków dla procesu redukcji, które wymagają intensywnej interakcji między gazem a ciałem stałym. Piec elektryczny obrotowy, mimo że jest wykorzystywany do przetwarzania metali, również nie nadaje się do bezpośredniej redukcji rud żelaza, ponieważ działa na zasadzie elektrycznego podgrzewania materiału, a nie na bezpośrednim usuwaniu tlenu. Takie podejścia mogą prowadzić do nieefektywności i większego śladu węglowego, co jest niezgodne z aktualnymi trendami w metalurgii, które dążą do zwiększenia efektywności energetycznej oraz redukcji emisji. Właściwe zrozumienie procesów redukcji i zastosowanych technologii jest niezbędne, aby unikać takich błędów w przyszłości.